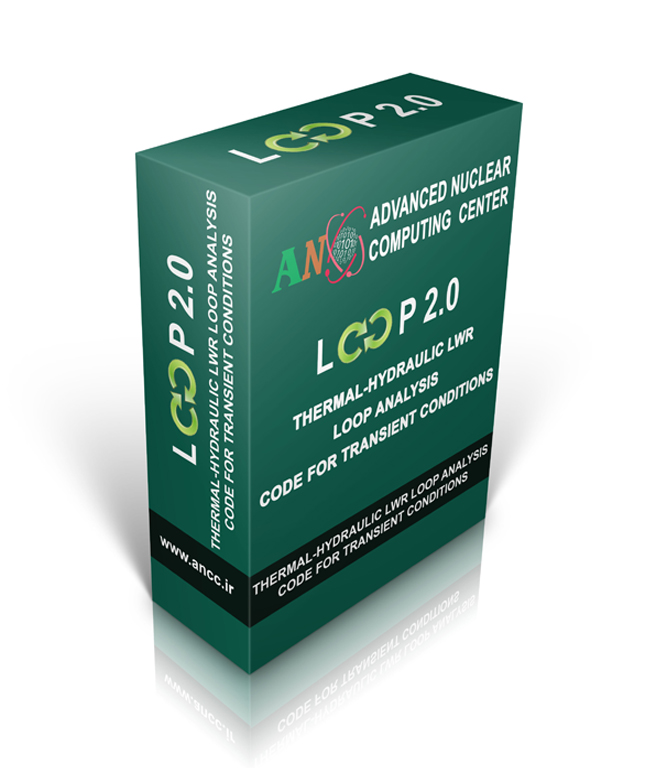
LOOP2.0
A computational software for Thermal-Hydraulic LWR Loops Analysis in Transient Conditions
DESCRIPTION
LOOP, is a computational software planned for thermal-hydraulic light water loops analysis in transient conditions. It is capable to model thermal-hydraulic systems by some standard components like channel, branch, junction, single volume, pump and steam generator. Transient conditions that can be model by this software are power transient in channels which contains heat structures, and also flow, temperature and pressure transients.
The software consists of a variety of solvers for treating homogenous and drift flux two phase flow models.
The entire system has been verified using various benchmarks and reference data, as well as, comparisons made mainly against RELAP5 outputs. Excellent agreements found in almost all cases which bring a meaningful trust for the users. Yet, V&V is still going on for more certitude.
METHODOLOGY
LOOP 2.0 benefits from the following well-proved approaches to deal with the mass, momentum and energy equations and constitutive relations:
- Control volume hydraulic model;
- DFM and HFM for two phase flow model;
- Sub-cooled nucleate boiling model,
- Pumps homologous model.
In addition, the heat conduction equation is solved via the simple but efficient finite difference approach which preserves needed speed along with sufficient accuracy for a wide range of real core thermal-hydraulic performances.
More development of the software like implement of heavy water thermodynamic properties is under investigations for future releases.
FEATURES
Followings are the major capabilities of LOOP 2.0:
- Capability of cylindrical or rectangular channel (contain fuel rods or fuel plates), branch, junction, single volume, pump and steam generator modeling.
- Ability to model mass flow, temperature and pressure transients of fluid flow.
- Ability to model power transients in channels with heat structure.
- Ability to choose arbitrary radial nodes in fuel, gap and clad.
- Heat generation in fuel clad and fuel gap as a part of generated heat.
- Axial power distribution factors along the fuel rod.
- Ability to model pump trip transient.
- User-friendly interface and graphical output display.
APPLICATIONS
LOOP 2.0 is especially developed for two main purposes:
- LWR and research reactor TH-Loops design and analysis, and,
- Other thermal-hydraulic systems design and analysis.
The software covers a wide range of needs for students, researchers and engineers in design and analysis of thermal-hydraulic problems. Model definition can be simply carried out and significant components and parameters can be obtained. LOOP 2.0 also empowers the user to observe output calculated parameters like temperature in fluid and heat structure, pressure, enthalpy, density, void fraction, equilibrium and non-equilibrium quality, heat convection coefficient along the time for each loop component.
LOOP 2.0 benefits from two different two-phase model for multi-channel thermal-hydraulic analyzer for detect boiling phenomena and estimate location of severe conditions in heat power generation and transportation. Also a look-up table is used to calculate critical heat flux ratio in channels or pipes with heat generation.
As the time always matters in design and analysis of industrial plants or even in purely academic interests, the code has been empowered with accelerating approaches to speed-up the calculations and to reduce the computational cost.
An interesting feature proposed for LOOP 2.0 is the ability to analyze more than one loop as simultaneously.
The last but not the least, would be display tools planned for the software to bring a rather suitable show of parameters for the user.